Welding is the backbone of structural integrity across countless construction projects. From heavy-duty frameworks to precise metalwork on-site, selecting the right welding process can impact efficiency, budget, and finished quality. Among the most commonly used welding methods in construction are MIG (Metal Inert Gas) and TIG (Tungsten Inert Gas). Each comes with its own set of advantages, limitations, and ideal applications.
Understanding the differences between MIG and TIG welders is essential for contractors, project managers, and field welders alike. At BC Industrial Supply, we provide both MIG and TIG equipment, along with repair services and consumables, ensuring crews have exactly what they need to keep projects moving.
Table of Contents
Core Differences Between MIG and TIG Welding
MIG welding, also known as Gas Metal Arc Welding (GMAW), uses a continuously fed wire electrode through a welding gun, creating an arc between the wire and the base metal. The process relies on shielding gas to protect the weld from contamination. MIG welding is known for its speed and ease of use, especially for beginners and in high-volume production settings.
TIG welding, or Gas Tungsten Arc Welding (GTAW), uses a non-consumable tungsten electrode to create the weld. Filler metal is added manually, and shielding gas (usually argon) is used to maintain weld purity. TIG offers superior precision, control, and cleaner welds, but requires more skill and is generally slower than MIG.
These fundamental differences create distinct advantages depending on the type of construction work being performed.
Productivity and Speed on the Jobsite
In construction environments where productivity is critical, MIG welding usually takes the lead. The continuous wire feed allows welders to maintain longer arcs and work faster across joints. This can be especially beneficial when welding thick materials or repeating the same welds on multiple sections.
TIG welding, by contrast, involves more deliberate, slower movements. The need to manually feed filler rod while maintaining arc stability makes TIG less suitable for high-speed production environments. However, for tasks where weld appearance or precise control is essential, speed becomes a secondary concern.
If time constraints and throughput are major concerns on a job, MIG will generally offer higher efficiency.
Weld Quality and Appearance
TIG welding consistently produces cleaner, more precise welds. The process allows for detailed control over heat input and filler application, which helps reduce spatter and post-weld cleanup. This makes TIG a better choice when appearance matters, such as with exposed architectural components or stainless steel fixtures.
MIG welds tend to have more spatter and may require cleanup, especially if shielding gas is disrupted or settings are not properly configured. However, MIG can still produce structurally sound and visually acceptable welds when performed correctly.
For projects requiring aesthetically clean seams or welds that will be visible and scrutinized, TIG welding has the edge.
Metal Types and Thickness
MIG welders handle a wider range of metal thicknesses and are often the preferred option for thicker sections of carbon steel, aluminum, and stainless steel. The wire-feed system can be adjusted for various materials, and MIG machines are typically easier to set up for different gauges.
TIG welders are better suited for thinner materials and specialty metals, including titanium, magnesium alloys, and thin-gauge stainless steel. The ability to precisely control amperage and filler material makes TIG ideal for preventing warping or burn-through on delicate components.
Choosing the correct method based on metal type and thickness can prevent project delays, minimize rework, and ensure long-lasting weld integrity.
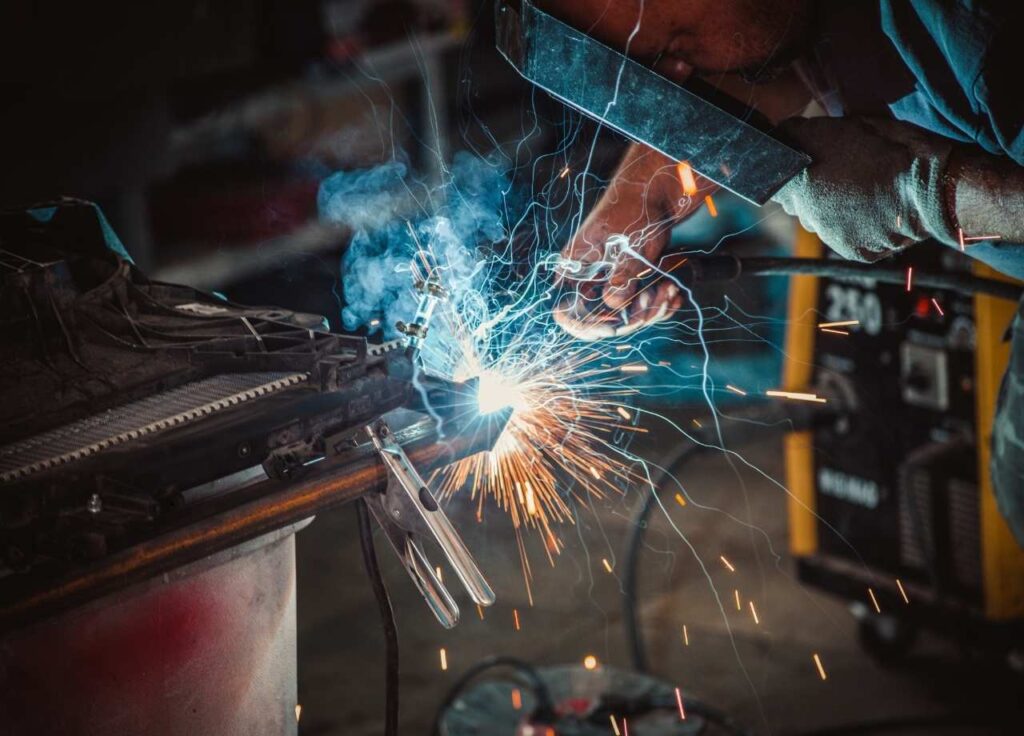
Skill Level and Training Requirements
MIG welding is often the first process taught to new welders due to its ease of use and short learning curve. Operators can become proficient relatively quickly, making MIG ideal for construction crews with varying levels of welding experience.
TIG welding demands significantly more hand-eye coordination and a deeper understanding of heat control and metallurgy. It takes longer to master and requires a higher level of concentration during execution. Mistakes in TIG welding are less forgiving, especially with heat-sensitive materials.
On construction sites with limited access to experienced welders, MIG welding offers a more practical solution. For specialty tasks or where certified TIG welders are available, TIG can deliver unmatched quality.
Equipment Portability and Setup
Construction projects often involve remote or mobile worksites, making portability a factor. MIG welding machines tend to be more rugged and easier to transport, especially compact models designed for jobsite use. Setup time is minimal, and many units come with synergic controls for quick parameter selection.
TIG welders typically involve more setup time, including separate gas cylinders, foot pedals, and additional accessories for controlling amperage. These setups can be more cumbersome to move and may not be ideal in tight or rugged environments.
When portability and quick deployment matter, MIG units have the advantage. For bench welding or controlled shop environments, TIG can be deployed without those limitations.
Cost Considerations for Construction Projects
MIG welding is often more cost-effective upfront and over the course of a project. The equipment tends to be less expensive, consumables are more readily available, and labor costs can be lower due to faster weld times. Maintenance on MIG machines is also generally straightforward.
TIG welding systems and consumables can cost more, and the process typically involves higher labor expenses due to slower speeds and the need for skilled technicians. However, TIG may reduce the need for post-weld finishing and rework, which can balance costs in high-precision applications.
Ultimately, project managers must evaluate whether speed and simplicity or precision and finish are more important to the job at hand.
Ideal Applications in Construction Settings
MIG welding is well-suited to structural steel, heavy equipment repair, and general fabrication tasks. It’s often used for welding I-beams, pipe, brackets, handrails, and steel frames where strength and speed are prioritized.
TIG welding is a better choice for detailed metalwork, stainless components, and tasks where joint integrity and appearance are critical. HVAC installations, handrails on public buildings, stainless countertops, and aluminum piping often call for TIG precision.
Larger construction projects may require both MIG and TIG capabilities at different stages, depending on the scope of work and material requirements.
Choosing the Right Welder for Your Team
There is no one-size-fits-all answer. The decision between MIG and TIG welders depends on project requirements, budget, crew experience, and metal type. Many construction operations benefit from having both capabilities available to address a broader range of tasks.
Project leads should assess which welding processes align best with productivity goals, aesthetic standards, and technical specifications. Equipment availability, repair support, and access to consumables also factor into the decision.
BC Industrial Supply carries both MIG and TIG welders, along with accessories, consumables, and repair services. Our team works closely with construction firms to match the right welding solution with the demands of each job. With nationwide shipping and local support, we help crews get the tools they need, fast.
Final Thoughts
MIG and TIG welding serve distinct but complementary roles in construction. MIG delivers speed, simplicity, and cost-efficiency for a wide range of structural tasks. TIG provides unmatched control, precision, and finish for more refined work. Understanding the strengths and limitations of each allows construction professionals to make informed decisions that improve workflow, reduce waste, and ensure high-quality outcomes.
When weld performance matters, knowledge is just as important as equipment. Taking time to match the right welding method to each task will keep projects on track and clients satisfied.