Laser welding is gaining attention across multiple industries for its precision, speed, and versatility. Contractors in fields like metal fabrication, automotive repair, and pipeline construction are evaluating whether laser welding machines offer tangible benefits over traditional methods such as MIG, TIG, or stick welding. Before making a substantial investment in equipment, it’s important to weigh the pros, cons, and practical applications of laser welding on job sites.
BC Industrial Supply carries a wide range of welding equipment, including laser systems and traditional arc welders, and provides expert guidance to help contractors choose the right tool for the job. Our fast shipping and responsive customer support ensure that your operation stays productive and equipped.
Table of Contents
What Is Laser Welding?
Laser welding uses a concentrated beam of light to fuse materials together. The laser generates intense heat in a localized area, allowing for high-precision welds with minimal heat distortion. This method can be used with or without filler metal and is compatible with a range of materials, including stainless steel, aluminum, titanium, and various alloys.
Unlike conventional arc welding, where heat is generated through an electric arc, laser welding is a non-contact process. The laser beam can be focused to a very fine point, enabling contractors to work on intricate components or hard-to-reach joints. This technology is also well-suited for automation, making it a valuable tool in high-volume manufacturing settings.
Advantages of Laser Welding for Contractors
One of the most talked-about benefits of laser welding is its precision. Contractors who work with thin metals or complex assemblies often deal with the risk of warping or burning through material when using traditional welders. Laser welding significantly reduces these risks thanks to its concentrated heat source and narrow weld zone.
Speed is another key advantage. Laser welders can complete welds much faster than conventional machines, especially when dealing with repetitive joints or long seams. This efficiency can be a game-changer for large-scale projects where labor time and productivity directly impact profit margins.
Laser welding also produces cleaner results. The narrow heat-affected zone means less spatter, fewer post-weld cleanups, and better-looking finished products. This is particularly useful in sectors where appearance and structural integrity are both critical.
The ability to weld dissimilar metals is a bonus that can solve challenges with specialty projects. When joining materials like copper to steel or titanium to aluminum, laser welding offers more control over thermal input, minimizing cracking or bonding issues.
Disadvantages to Consider
Despite its advantages, laser welding is not without drawbacks. The initial cost of a laser welding machine is significantly higher than that of a MIG or TIG welder. While prices have come down in recent years, contractors should be prepared for a capital investment that can run into tens of thousands of dollars.
Another consideration is the learning curve. Operators need proper training to handle laser equipment safely and effectively. The machine settings are more complex than those of a standard welder, and improper use can lead to subpar welds or even damage to the materials.
Laser welding also requires precise joint fit-up. Gaps that a MIG welder might bridge without issue can become a problem in laser welding, especially without filler metal. This makes the process more demanding in terms of material preparation and fixturing.
Maintenance and repair of laser systems can be more expensive. The components, including fiber-optic cables, cooling units, and laser sources, are sensitive and must be kept clean and calibrated. If something fails, downtime can be longer unless you have access to specialized service technicians.
Use Cases Where Laser Welding Excels
Laser welding shines in applications where speed and precision are vital. Contractors working in custom fabrication shops, particularly those producing stainless steel countertops, cabinetry, or decorative structures, benefit from the clean, controlled welds laser systems produce.
Automotive repair specialists also find value in laser welding. When dealing with thin body panels or high-performance exhaust systems, conventional welding may be too aggressive. Laser welding minimizes burn-through and preserves the original geometry of the part.
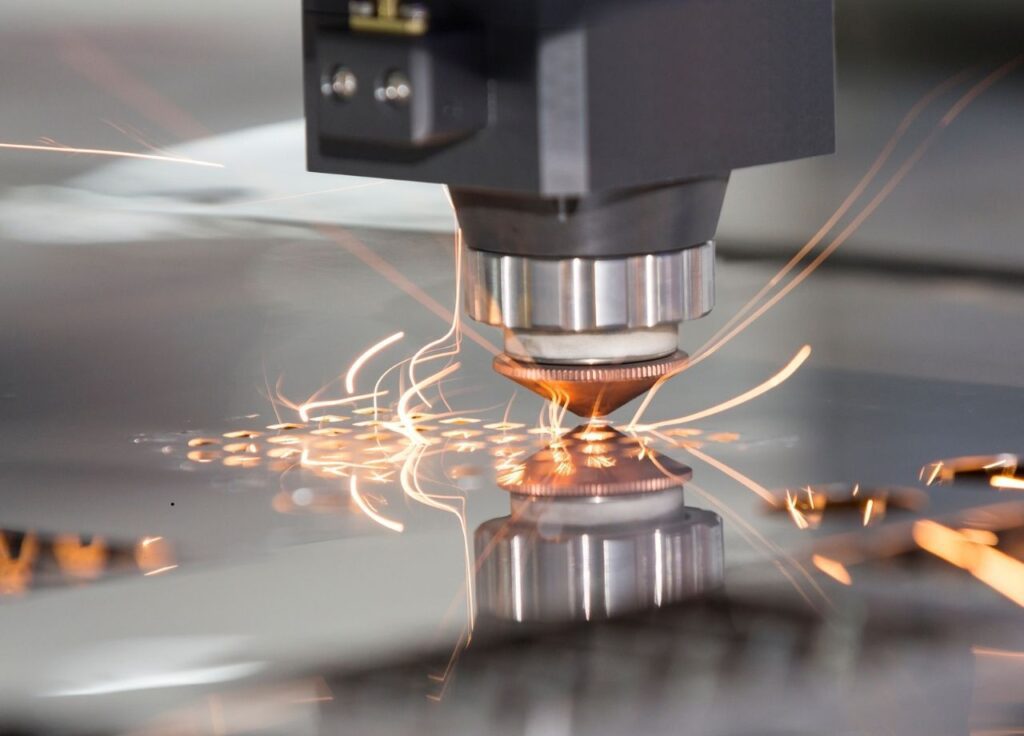
Pipeline contractors use laser welding for cladding and repairs, particularly on high-alloy pipes exposed to corrosive environments. The process provides the ability to deposit a corrosion-resistant layer with minimal dilution into the base material.
Electronics and medical device manufacturers frequently use laser welding for assembling components that must meet tight tolerances. While this may be outside the typical scope for most contractors, those involved in highly specialized or niche manufacturing may find laser systems essential.
Laser Welding vs. Traditional Methods
The comparison between laser and traditional welding methods depends heavily on the job at hand. For high-volume work or intricate components, laser welding offers unmatched speed and consistency. However, for structural steel fabrication, heavy-duty repair, or jobs requiring portability and flexibility, stick and MIG welding remain the go-to tools.
TIG welding still offers the best control for delicate work requiring filler metal. MIG is faster and more forgiving for general fabrication, while stick welding handles dirty or outdoor conditions better. Laser welding, by contrast, requires a clean environment and well-prepared joints, making it less forgiving in the field.
The best approach may be to view laser welding as a complement rather than a replacement. Contractors who add laser systems to their arsenal often retain traditional welders for rough work or first-pass welds and use laser welding for finishing or specialty applications.
Key Considerations Before Investing
Before purchasing a laser welding machine, contractors should evaluate their workflow, materials, and project volume. If most jobs involve structural steel, heavy wall pipe, or outdoor installations, traditional arc welding may be more practical. If precision, speed, and material variety are top priorities, laser welding deserves serious consideration.
Also consider the availability of trained personnel. Investing in laser welding means either hiring operators familiar with the technology or training current staff. Manufacturers and equipment suppliers often offer certification programs to help ease the transition.
Another factor is space. Laser welding machines require a stable, clean environment with room for ventilation and cooling systems. Mobile use is possible with fiber laser units, but setup is more involved compared to wheeling out a stick welder.
Final Thoughts
Laser welding offers contractors an opportunity to boost productivity, improve quality, and take on more technically demanding work. While it comes with a steeper price tag and higher expectations for operator skill and preparation, the benefits can justify the investment for shops handling high-precision or high-volume work.
Contractors who understand their needs, project types, and long-term goals will be in the best position to determine whether laser welding fits their operation. When chosen and used wisely, it can become a high-value addition to any professional welding lineup.