When heavy-duty work calls for fastening or loosening bolts under high torque, an impact wrench becomes a vital part of the job. Whether it’s assembly, maintenance, or fabrication, selecting the right impact wrench affects both performance and productivity. The wrong tool can slow down a job or even damage materials and fasteners. That’s why professionals across construction, manufacturing, and mechanical industries rely on high-quality tools tailored to their specific tasks.
At BC Industrial Supply, we help customers across the U.S. find the right tools for the job, whether it means buying new impact wrenches, renting equipment for short-term use, or getting repairs done quickly. But when it comes to choosing the right tool, it helps to understand what makes one impact wrench different from another.
Table of Contents
Understanding Impact Wrench Types
Industrial-grade impact wrenches come in several types, and each is suited to a particular application. The three most common types are pneumatic (air), electric (corded), and cordless (battery-powered).
Pneumatic impact wrenches are known for their high torque output and are commonly used in manufacturing plants and heavy machinery shops. These wrenches are powered by compressed air, which makes them lightweight and extremely durable. They require an air compressor, which may not be ideal for all environments, but for high-volume, repetitive jobs, they offer consistent performance over long periods.
Corded electric impact wrenches draw power from an outlet, offering steady torque without the need for air hoses or batteries. These are useful in workshops where mobility isn’t a concern, and uninterrupted power is a priority. While not as commonly used in mobile or remote jobs, they still offer significant value in controlled environments.
Cordless impact wrenches are growing in popularity for their convenience and portability. With improvements in battery technology, modern cordless tools deliver impressive torque and run time. These are ideal for field service, automotive repair, and situations where flexibility and access are more important than extended duty cycles.
Assessing Torque Requirements
Torque is the primary performance metric for any impact wrench. Measured in foot-pounds (ft-lbs), torque represents the tool’s ability to twist and tighten or loosen a fastener. For industrial use, torque needs can vary significantly.
Light-duty jobs, like automotive work or small machine assembly, might only require 100 to 300 ft-lbs. In contrast, structural steelwork, heavy equipment maintenance, and rail or shipyard work often demand 1,000 ft-lbs or more. Choosing a tool that matches your torque requirement is critical—using a tool with too little power can stall the job, while too much torque can strip threads or break fasteners.
It’s also worth considering variable torque settings or a tool with multiple speed settings. This allows for greater control in situations where torque precision is necessary, such as working with delicate components or sequential tightening procedures.
Drive Size and Compatibility
The drive size refers to the square nub on the tool that attaches to the socket. Common drive sizes include ¼”, ½”, ¾”, and 1”. The larger the drive size, the more torque the tool can generally handle. In heavy industrial environments, ¾” and 1” drives are often preferred because they accommodate larger fasteners and offer higher strength.
Matching the drive size with your existing sockets and accessories is essential. Using reducers or adapters can create weak points that may fail under high torque. For long-term durability and safety, it’s best to use the correct size drive for the application.
Considering Ergonomics and Operator Fatigue
Impact wrenches generate vibration and noise during use, which can contribute to operator fatigue over time. Weight, grip design, and overall balance of the tool play a major role in day-to-day comfort and productivity. This is especially important in tasks requiring repetitive use or overhead work.
Look for features like rubberized grips, vibration dampening technology, and lightweight materials that reduce strain without compromising durability. Some tools also come with adjustable handles or swivel air inlets to allow better maneuverability in tight spaces.
Noise level is another factor worth attention. Pneumatic wrenches tend to be louder than electric ones. In noise-sensitive environments or when operating indoors for extended periods, consider tools with mufflers or lower decibel ratings.
Power Source Availability and Jobsite Conditions
Choosing the right impact wrench also depends on your work environment. In fixed facilities with existing air infrastructure, pneumatic tools make sense. On construction sites without reliable electricity or compressed air, cordless models provide unmatched flexibility.
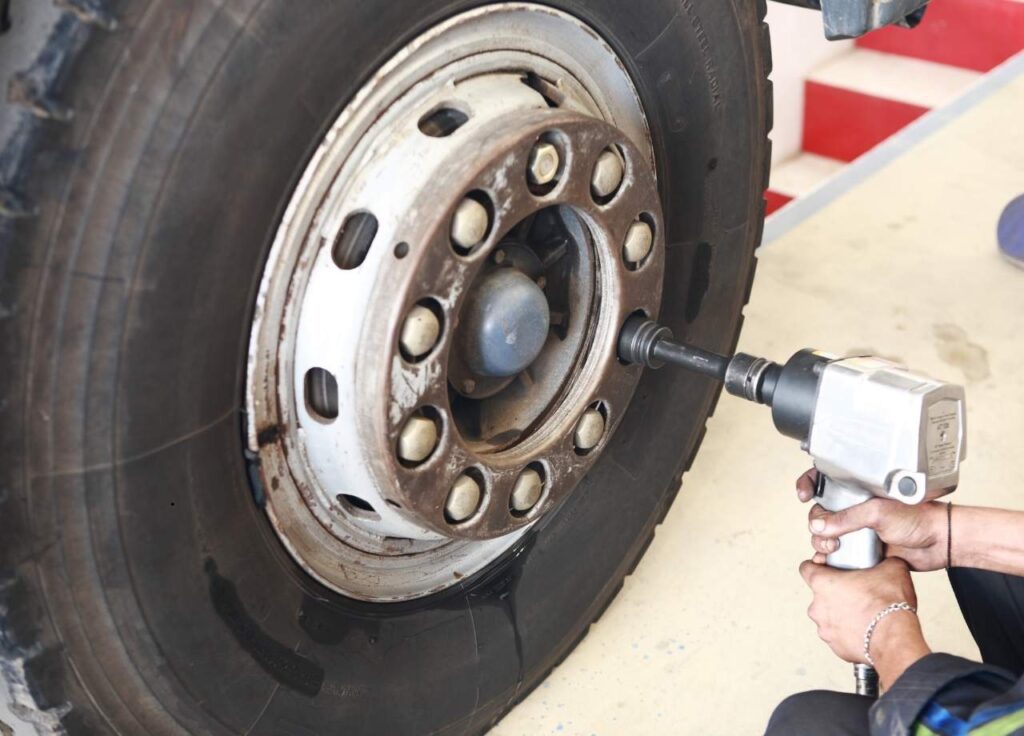
Weather and jobsite conditions should also guide your decision. Outdoor work in wet or dusty environments may call for tools with sealed housing and weather-resistant features. Cold weather performance is another consideration, as battery-powered tools can experience reduced run time in freezing conditions.
Duty Cycle and Intended Use
Not all impact wrenches are built for the same level of use. Light-duty tools may be sufficient for occasional maintenance or general repair, but for continuous use in production lines or assembly operations, you’ll need a heavy-duty model with industrial-grade components.
Check the manufacturer’s duty cycle ratings and intended use descriptions. Overworking a light-duty tool can shorten its lifespan and lead to unplanned downtime. On the other hand, using a high-capacity industrial tool for basic applications may add unnecessary weight and cost.
Maintenance and Serviceability
Even the best impact wrenches will need maintenance over time. Ease of serviceability can be a deciding factor when selecting equipment. Some models offer tool-free access to internal components or have wear parts that can be quickly replaced on-site.
Check availability of replacement parts, and whether the manufacturer offers service manuals or technical support. Partnering with suppliers who provide repair services, like BC Industrial Supply, can extend the life of your equipment and reduce downtime when issues arise.
Lubrication is another maintenance factor. Pneumatic tools, for instance, often require regular oiling and occasional cleaning of air filters. Understanding these maintenance needs upfront helps avoid costly surprises later.
Cost vs. Performance Balance
Budget always plays a role, but the lowest price doesn’t always translate to the best value. Consider total cost of ownership, which includes initial investment, maintenance, expected lifespan, and potential downtime. A mid-range tool that lasts for years under regular use can be a better investment than a low-cost tool that needs replacing after a few months.
Evaluate what features are essential versus optional. Paying extra for a brushless motor, advanced torque control, or a rugged case might be worth it depending on your application.
Final Thoughts
Selecting the right impact wrench for industrial use involves more than just picking the strongest tool on the shelf. It requires a clear understanding of your job requirements, power source availability, torque needs, and ergonomic considerations. By taking the time to assess these factors, you can equip your team with tools that deliver better results, safer operation, and long-term reliability.
For businesses looking to outfit an entire crew or tackle specialized projects, working with an experienced supplier can streamline the process. Whether you need a short-term rental, a long-term purchase, or dependable repair services, having a partner like BC Industrial Supply ensures you get what you need to keep the work moving forward.